Nitrogen is essential across industries like semiconductors, electronics, food and beverage, pharmaceuticals, laser cutting, and metal fabrication. For laser cutting and metal fabrication in particular, high-purity nitrogen ensures oxidation-free cuts and welds, leading to superior product quality. To meet these demands efficiently and sustainably, on-site nitrogen generation has become a preferred solution due to its cost-effectiveness, with Pressure Swing Adsorption (PSA) technology at the forefront.
PSA systems are available in two primary designs: Traditional twin-tower systems and modern modular systems, such as NOVAIR’s Nitroswing. This article examines how modular PSA nitrogen generators stack up against traditional twin-tower systems, focusing on key factors like flexibility, efficiency, and cost-effectiveness.
Key Comparisons Between Modular and Twin-Tower PSA Systems
1. Flexibility and Scalability
In an ever-changing industrial landscape, the ability to adapt to fluctuating demands is a key driver of operational efficiency. Selecting the right nitrogen generation system can significantly impact a company’s ability to remain agile.
Traditional Twin-Tower Systems
- Fixed capacity limits.
- Scaling often requires over-designing the initial system or purchasing a new unit.
Modular Systems (e.g., NOVAIR Nitroswing)
- Ideal for industries like metal fabrication, where nitrogen needs can vary significantly.
- Easily scalable by adding or removing modules to match demand.
Advantage: Modular systems provide unmatched flexibility, letting businesses adapt to changing production needs without overcommitting resources.
2. Energy Efficiency
Energy consumption is a critical factor in operational costs, particularly for industries with high nitrogen demands. Efficient systems can lead to substantial savings over time.
Traditional Twin-Tower Systems
- Operate continuously, even when demand is low, leading to wasted energy.
Modular Systems
- Activate specific modules as needed, significantly reducing energy consumption.
- Particularly beneficial for energy-intensive applications like laser cutting, which demand high purity and flow rates.
Advantage: Modular systems minimize energy use, offering substantial savings for high-demand operations.
3. Maintenance and Downtime
Reliable nitrogen supply is vital for many industries. Downtime can lead to costly delays. The maintenance requirements of a system can make a big difference in operational continuity.
Traditional Twin-Tower Systems
- Maintenance often causes prolonged downtime, disrupting nitrogen supply.
- A failure in one tower can halt the entire system.
Modular Systems
- Ensures generally uninterrupted nitrogen supply, even when servicing, which is critical for industries like laser cutting.
- Individual modules can be serviced without halting overall production.
Advantage: Modular systems enhance uptime, reducing costly interruptions for nitrogen-dependent operations.
4. Footprint and Installation
Space constraints are often a challenge for businesses, particularly in workshops and factories. The design and installation requirements of a nitrogen generator play a crucial role in its suitability.
Traditional Twin-Tower Systems
- Require large, fixed installations.
- Are a challenge to fit into facilities with limited or irregular space.
Modular Systems
- Compact and lightweight, allowing for flexible configurations.
- Seamlessly integrate into existing setups, even in constrained workshops.
Advantage: Modular systems maximize space efficiency, making them a smart choice for industries with tight floor plans.
5. Cost Considerations
Balancing initial investment and long-term savings is essential when choosing industrial equipment. A cost-effective nitrogen generator can provide financial flexibility for future growth.
Traditional Twin-Tower Systems
- High upfront costs due to large-scale equipment.
- Expensive upgrades or expansions.
Modular Systems
- Lower initial investment and cost-effective scalability.
- Incremental upgrades reduce the need for over-purchasing capacity.
Advantage: Modular systems offer a budget-friendly solution, particularly for industries with evolving production demands like laser cutting.
Real-World Results from Modular PSA Adoption
Case Studies
Laser Cutting
A precision manufacturer replaced a twin-tower generator with the NOVAIR Nitroswing modular system. The result? A 30% reduction in energy consumption and zero downtime during peak operations. The scalability of the system enabled seamless handling of increased client demands.
Metal Fabrication
A metalworking firm saw operational costs drop by 20% within a year of switching to a modular system. The ability to add modules as needed allowed the company to expand its contracts without overextending its budget.
Food Packaging
A food packaging company reduced nitrogen production costs by 25% in six months. The modular system ensured compliance with strict industry standards while improving cost efficiency.
Pharmaceutical Manufacturing
A pharmaceutical company scaled nitrogen production by 40% over three years without replacing its core infrastructure, effortlessly meeting regulatory and production demands.
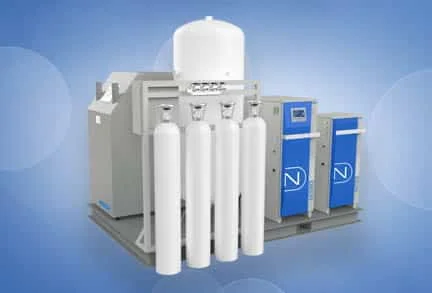
Conclusion
Modular PSA nitrogen generators, like the NOVAIR Nitroswing, provide significant advantages over traditional twin-tower systems. Their scalability, energy efficiency, and reduced downtime make them ideal for industries like laser cutting and metal fabrication, but also many others where high-purity nitrogen is a non-negotiable necessity. Companies looking to optimize nitrogen production and adapt to dynamic market demands should consider modular systems as a future-proof solution.
For more information on modular PSA technology, contact NOVAIR USA at 716-564-5165 or visit www.novair-usa.com.